A 3D printer made entirely at EPFL
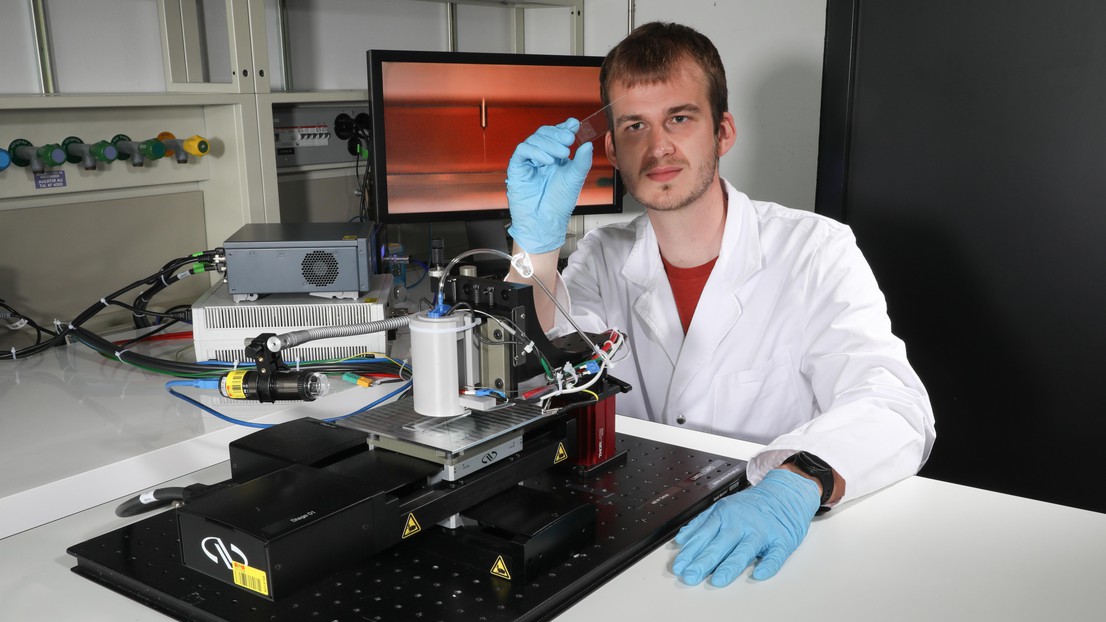
© Alain Herzog 2021 EPFL
EPFL students have made a high-performance 3D printer that can print structures measuring just a few microns across.
Six months ago, EPFL professors Christophe Moser and Jürgen Brugger were in the market for a printer. But all the options were either too expensive or not up to standard. So they decided to build their own: an ultra-thin filament printer capable of printing in two and three dimensions. “We had some funding from EPFL, but we couldn’t find a melt electrowriting (MEW) printer that met our requirements,” says Moser. The pair decided to put the School’s students and engineers on the case. “We started from square one,” explains the prototype’s designer Deeke Ehmen, an engineer at the Microsystems Laboratory 1, part of EPFL’s School of Engineering (STI). “We had to learn how MEW technology works and what materials we needed to use.”
Building a printer from scratch is a feat of engineering in its own right. But the machine’s capabilities are equally impressive: it can print parts measuring between 1 and 10 microns in diameter. This compares with a limit of 100 microns for conventional filament 3D printers. Another stand-out feature of the new printer is its speed: it takes around two minutes to make a 20 x 20 mm structure. “It all depends what you’re printing, but it’s generally done by the time you’ve finished your coffee,” jokes Ehmen.
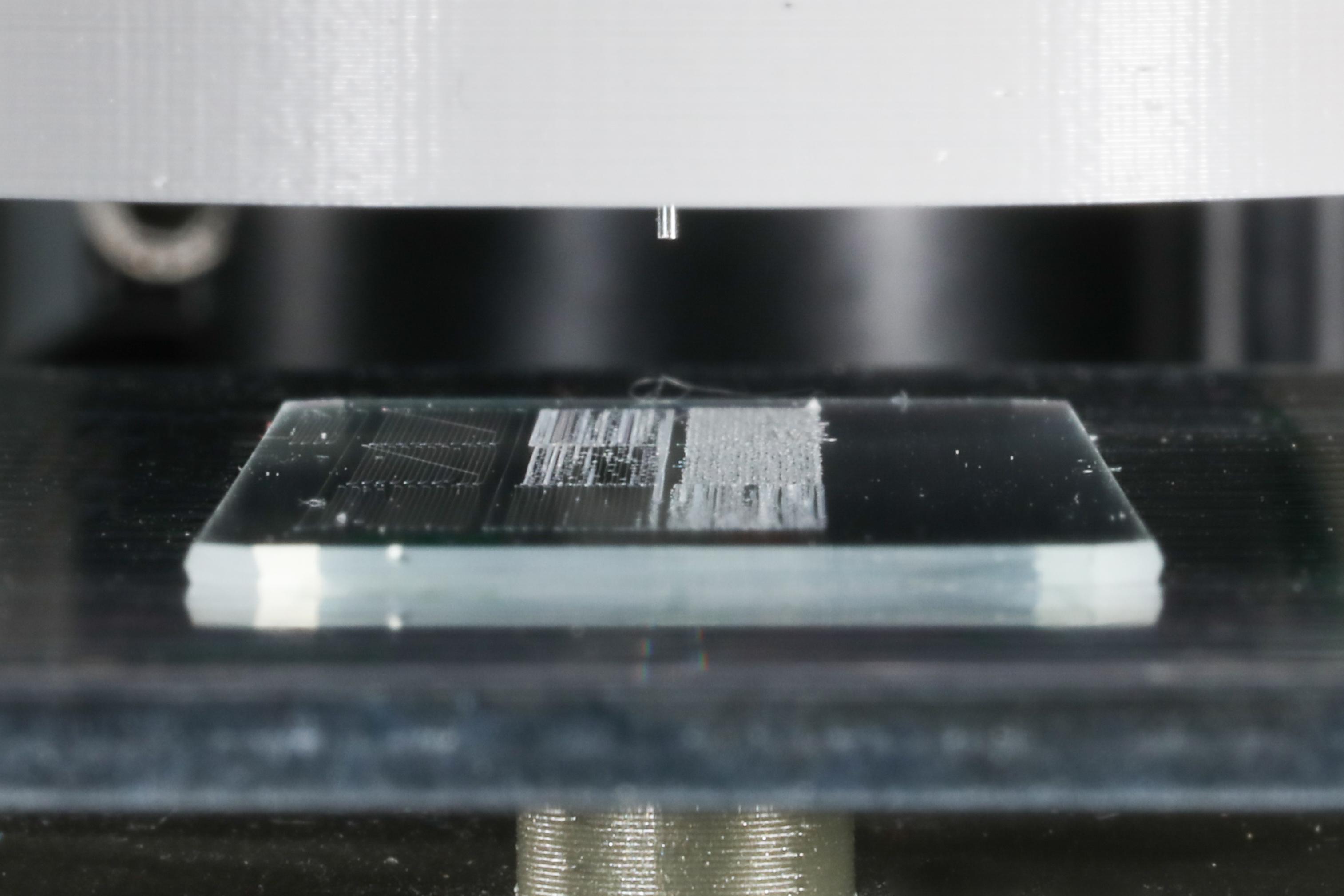
Complete control
For the researchers, having their own printer is the best of both worlds. Because they built it themselves and know exactly how it works, configuring the machine comes as second nature. It also means they can adjust it to different applications. “It’s the perfect tool for both teaching and scientific research,” says Moser. “We’ve developed a basic system, which we can then adapt and fine-tune to suit particular materials or requests. Building our own printer also made financial sense: buying a similar model could have set us back as much as 70,000 Swiss francs. But having complete control over the system was the decisive factor.”
The machine offers an array of possibilities, primarily in biology, where its applications include making scaffolding for tissues and cell cultures, as well sensors and biomedical devices. “The fact that we can use so many materials, including all types of plastic, means that, in theory, we could print all sorts of different products,” explains Ehmen.
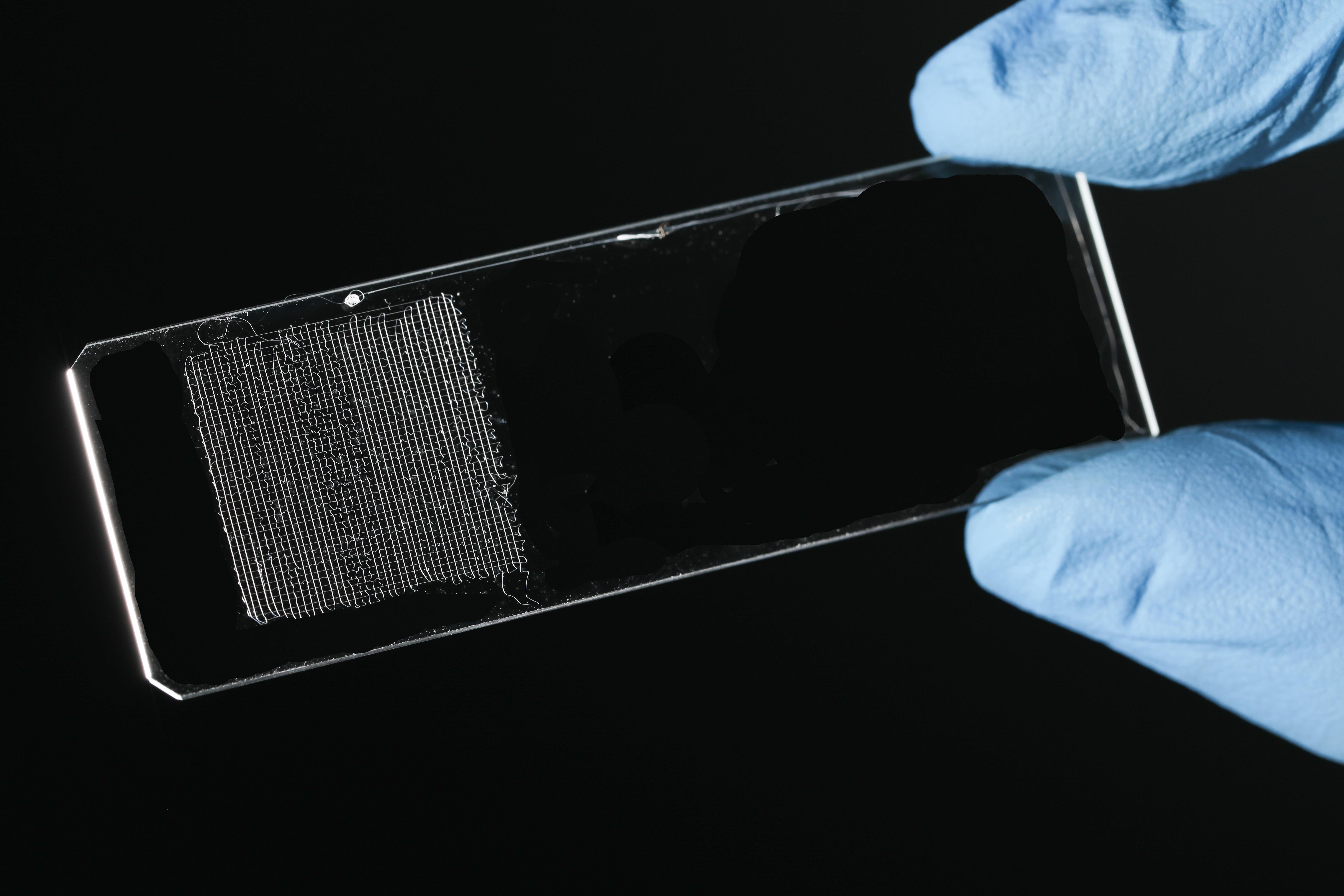
© Alain Herzog 2021 EPFL
The team was assisted by Paul Dalton, the inventor of MEW technology. In the future, they plan to use the printer as both a research tool and a teaching resource in advanced additive manufacturing classes. “The printer can be used by researchers from EPFL and other Institutions,” says Brugger. “We’re always open to collaborating with new people.”