Sustainable plastics from agricultural waste
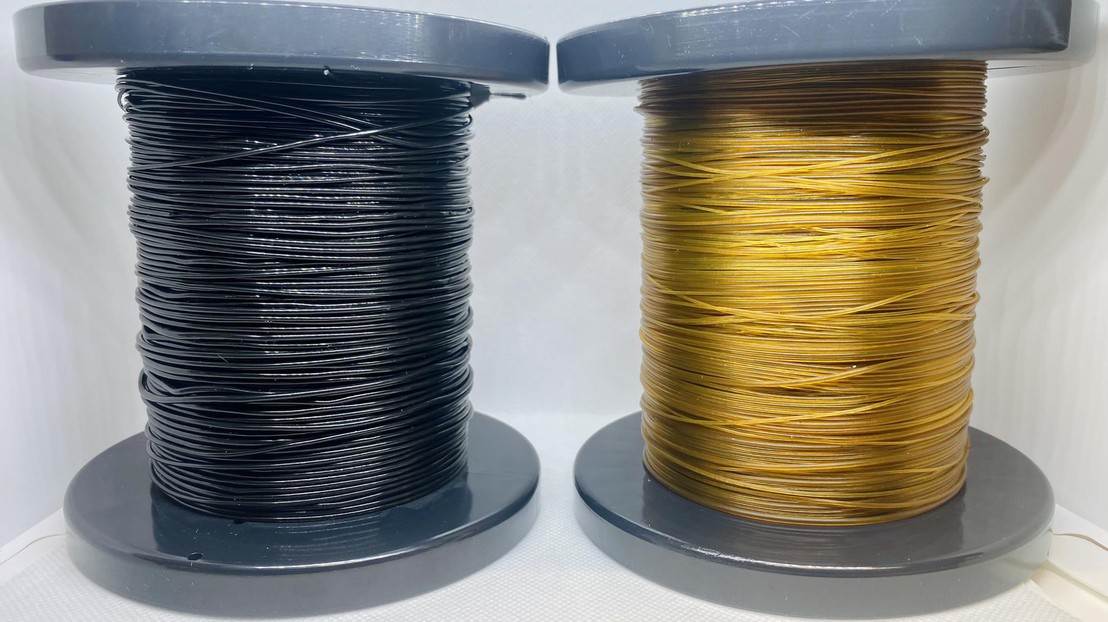
The dyed and natural polyamide fibers after extrusion. Credit: Lorenz Manker/EPFL
EPFL scientists have developed a sustainable method to make high-performance plastics from agricultural leftovers, turning them into valuable materials.
In our rapidly industrialized world, the quest for sustainable materials has never been more urgent. Plastics, ubiquitous in daily life, pose significant environmental challenges, primarily due to their fossil fuel origins and problematic disposal.
Now, a study led by Jeremy Luterbacher's team at EPFL unveils a pioneering approach to producing high-performance plastics from renewable resources. The research, published in Nature Sustainability, introduces a novel method for creating polyamides – a class of plastics known for their strength and durability, the most famous of which are nylons – using a sugar core derived from agricultural waste.
...we get similar results but use a sugar structure, which is ubiquitous in nature and generally completely non-toxic, to provide rigidity and performance properties.
The new method leverages a renewable resource, and also achieves this transformation efficiently and with minimal environmental impact.
“Typical, fossil-based plastics need aromatic groups to give rigidity to their plastics – this gives them performance properties like hardness, strength and high temperature resistance,” says Luterbacher. “Here, we get similar results but use a sugar structure, which is ubiquitous in nature and generally completely non-toxic, to provide rigidity and performance properties.”
Lorenz Manker, the study’s lead author, and his colleagues developed a catalyst-free process to convert dimethyl glyoxylate xylose, a stabilized carbohydrate made directly from biomass such as wood or corn cobs, into high-quality polyamides. The process achieves an impressive atom efficiency of 97%, meaning almost all the starting material is used in the final product, which drastically reduces waste.
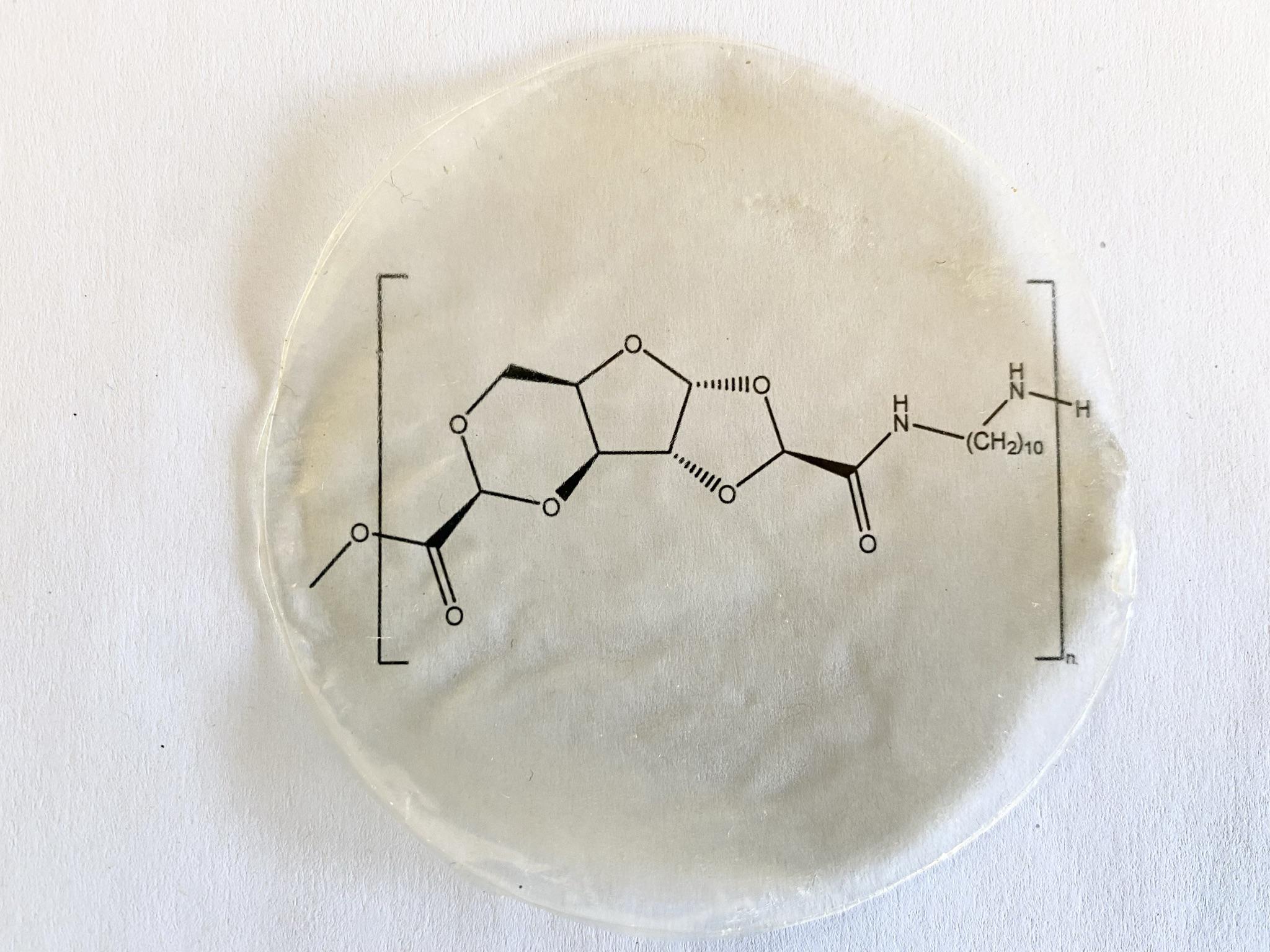
The bio-based polyamides exhibit properties that can compete with their fossil counterparts, offering a promising alternative for various applications. What's more, the materials demonstrated significant resilience through multiple cycles of mechanical recycling, maintaining their integrity and performance, which is a crucial factor for managing the lifecycle of sustainable materials.
The potential applications for these innovative polyamides are vast, ranging from automotive parts to consumer goods, all with a significantly reduced carbon footprint. The team's techno-economic analysis and life-cycle assessment suggest these materials could be competitively priced against traditional polyamides including nylons (e.g. nylon 66), with a global warming potential reduction of up to 75%.
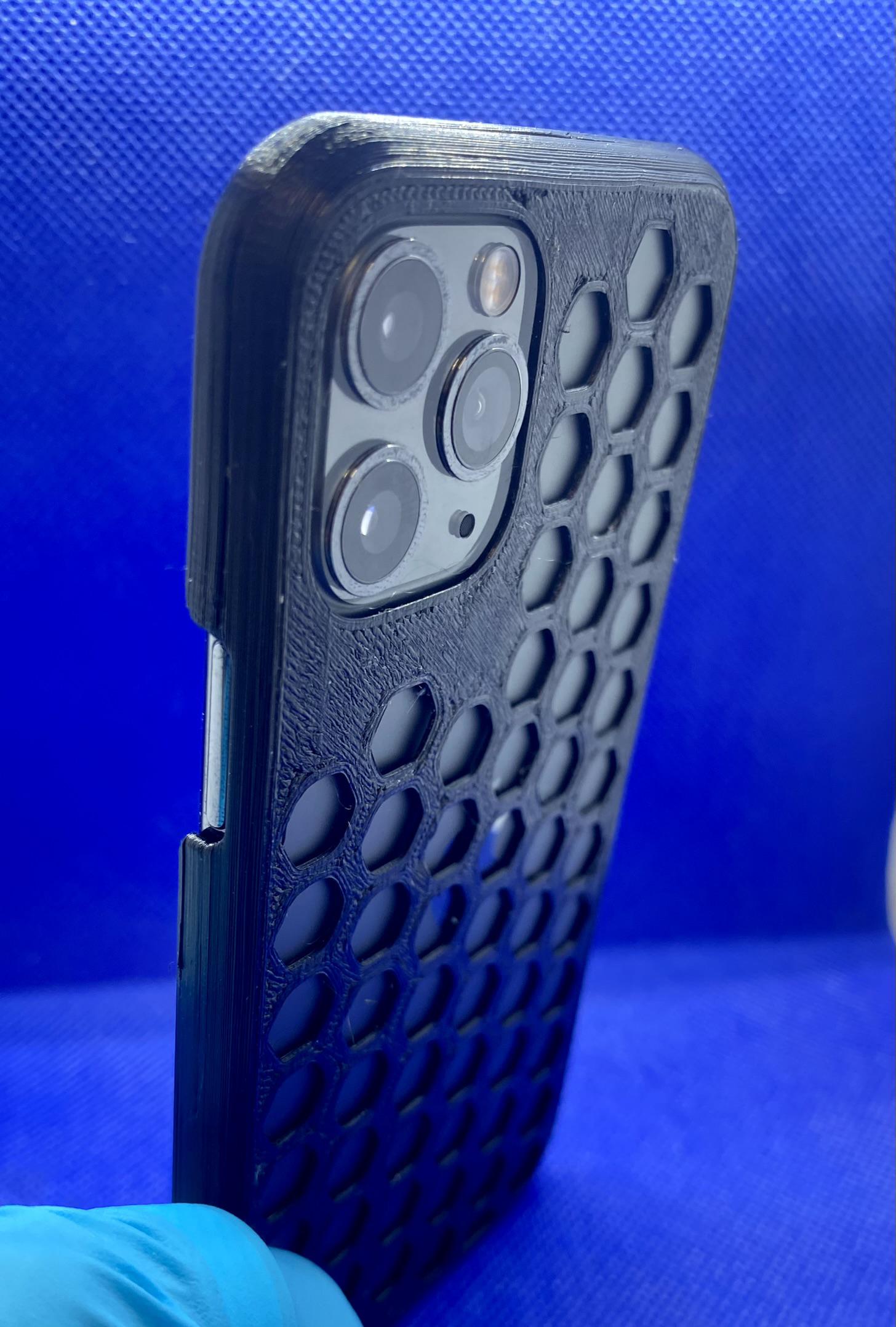
The production of these materials is now being scaled up by the EPFL spin-off, Bloom Biorenewables, in an effort to get them into the market.
Other contributors
- University of Applied Sciences and Arts Western Switzerland
- EPFL Institute of Materials
- EPFL Valais-Wallis
- The University of Manchester
Swiss National Science Foundation (SNSF)
National Centres of Competence (NCCR) Catalysis
Marie Sklodowska-Curie grant
EPFL
Industrial Strategy Challenge Fund (ISCF) Smart Sustainable Plastic Packaging
Sustainable Materials Innovation Hub
Lorenz P. Manker, Maxime A. Hedou, Clement Broggi, Marie J. Jones, Kristoffer Kortsen, Kalaiyarasi Puvanenthiran, Yildiz Kupper, Holger Frauenrath, François Marechal, Veronique Michaud, Roger Marti, Michael P. Shaver, Jeremy S. Luterbacher. Performance polyamides built on a sustainable carbohydrate core. Nature Sustainability 13 March 2024. DOI: 10.1038/s41893-024-01298-7